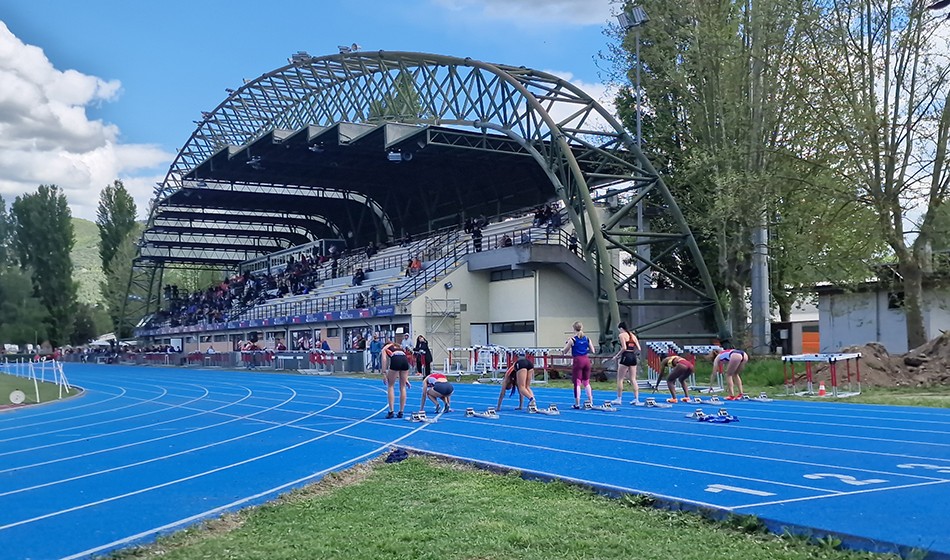
A fact-based comparison of two types of synthetic athletics tracks
The choice of track system has a direct impact on the longevity, performance and sustainability of a sports facility. While in-situ (poured) tracks have been a global standard at international events, training facilities, and stadiums for decades, prefabricated systems are often chosen for high-profile competitions primarily due to marketing or partnership-related reasons. A neutral look at the technical facts reveals significant differences.
Certification and Origin
According to the publicly available certification list by World Athletics, there are currently 35 certified prefabricated track systems. Notably, the vast majority of these systems originate from Asia, particularly China. Only two certified prefabricated systems currently come from a European manufacturer (Italy). This stands in contrast to in-situ systems, which are predominantly developed and manufactured in Europe and are backed by a long-standing tradition of high-quality, durable surface solutions.
Hardness, Elasticity and Common Misconceptions
There is a belief that prefabricated tracks are harder and therefore preferred by athletes under the assumption that a harder track is faster. However, this is a misconception:
- A hard track is not automatically faster. What matters is the balance between hardness and elasticity. Only when both properties are optimally aligned can a track offer maximum performance.
- All World Athletics-certified tracks must comply with defined limits for force reduction, the key metric used to assess hardness. The acceptable range lies between 35% (hard) and 50% (soft) force reduction. This means any certified track – whether in-situ or prefabricated – meets these criteria and can be delivered with a desired hardness level (eg, near the lower limit of 35%) if required.
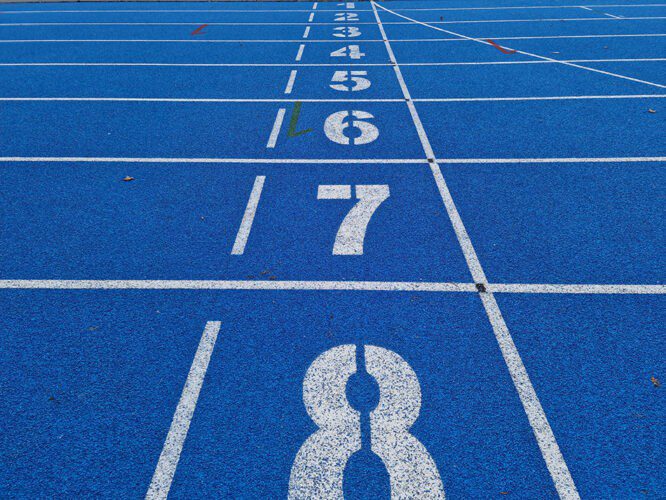
The real challenge lies in material aging. Tracks “live” – they harden over time. Prefabricated systems exhibit significantly faster hardening than in-situ tracks. For major competitions like the Olympic Games, tracks are often installed with a force reduction of 35% (the hardest permissible value). However, in many cases, this value falls outside the allowable range after just one year. Since stadiums are typically re-certified only every four years, such deviations are often only discovered later.
Additionally, the spikes on athletes’ shoes act like awls on hardened prefabricated surfaces. The loss of elasticity combined with surface rigidity can lead to significant material loss in the top layer, especially in high-wear areas.
Durability and Maintenance
A key advantage of in-situ tracks is their longer lifespan and lower maintenance costs. The seamless on-site installation creates a homogeneous surface with consistent performance across all lanes. Prefabricated tracks, on the other hand, are composed of rolls of material that are glued together. This leads to several structural issues:
- Weakness at joints: The glued seams are particularly vulnerable to mechanical stress and weather conditions. These areas often deteriorate first. Temperature and humidity fluctuations cause expansion and contraction. Unlike in-situ systems, which behave as a single unit, prefabricated systems develop tension at the roll interfaces – often leading to visible joint openings. A standard prefabricated track includes at least 4km of seams.
- Uneven stress distribution: Due to track geometry (eg, the tighter curve of lane one compared to lanes eight or nine), prefabricated systems can exhibit uneven tension, leading to reduced longevity and premature damage.
Another major benefit of in-situ systems is the ability to retop the track surface, applying a new wear layer. This offers a sustainable method of renewing the track while conserving resources and reducing CO₂ emissions. Prefabricated tracks can only be retopped using an in-situ system – retopping with another prefabricated layer is technically not feasible. As a result, operators of prefabricated tracks must switch to in-situ solutions when renewing the surface, which increases complexity and poses technical challenges when combining the two systems.
Repairs are also a major concern. Friction from starting blocks at specific locations (eg, 100m, 110m hurdles, 200m, 400m starts) often results in early wear on prefabricated tracks. These areas must be replaced after just a few years, requiring patchwork repairs. The resulting surface inconsistencies – in terms of force reduction and energy return – can have a noticeable impact on athlete biomechanics, especially when located within the oval where most of the running occurs.
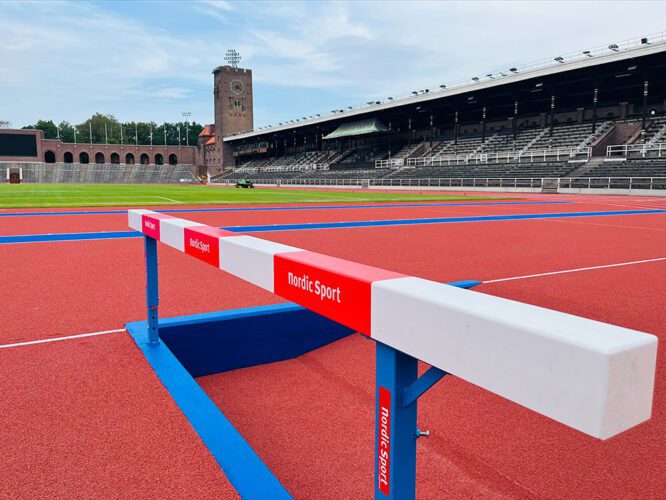
Sustainability
Modern in-situ systems are increasingly designed to meet high environmental standards, including the use of recycled materials and low-emission binders. Prefabricated tracks tend to lag behind in sustainability due to their energy- and material-intensive production, long-distance shipping (often from Asia) and limited recyclability.
This is reflected in the decisions of countries with ambitious environmental policies: Germany, Norway, and Switzerland rarely use prefabricated systems for their sports facilities, instead favoring in-situ tracks. These decisions are driven by a combination of ecological, technical, and economic advantages.
Market Dynamics and Partnerships
It is striking that prefabricated tracks are sometimes selected for global top-tier events, even though they objectively do not meet the highest standards of quality and sustainability. In many cases, this can be attributed to marketing partnerships and sponsorship agreements. This raises questions – especially in view of World Athletics’ high standards – about the influence of commercial relationships on surface selection.
Conclusion
The facts clearly show that in-situ tracks offer significant advantages over prefabricated systems in terms of:
- Durability and retoppability
- Uniform performance without structural weak points
- Sustainability through local production and resource-efficient renewal
- Stable hardness and elasticity values over time
For federations, cities and facility operators, it is worth looking beyond well-known brand names and sponsorships and instead focusing on objective quality criteria – for the benefit of the athletes, the environment and long-term economic viability.