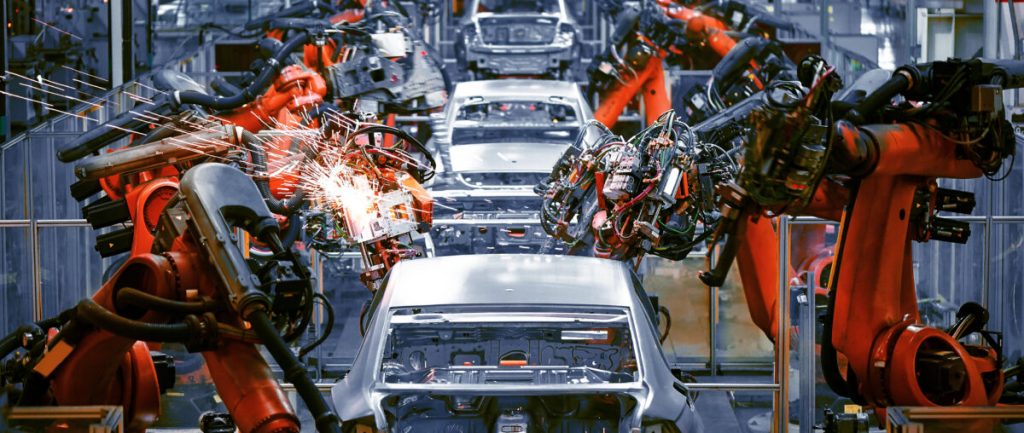
Subject experts and industry stakeholders outline some effective methods for bringing down the cost of electric vehicle production. By Will Girling
Electric vehicles (EVs) are arguably better than they’ve ever been: consumers now have access to a greater variety of models at different price points and range capabilities to suit their needs. However, manufacturing these products profitably has been an ongoing challenge for automakers. Few are operating in the black, and some are seeing mounting losses from their EV activities.
Trade wars, geopolitical shifts, and slower-than-anticipated uptake have all conspired to make EV production more difficult and expensive than many initially expected. Q1 2025 reports from Volkswagen and Ford indicate they still lose thousands of dollars per EV sold. Meanwhile, even those that have made progress face worsening conditions: General Motors’ EV line-up was finally “variable profit positive” in Q4 2024, but US import tariffs could reshape key supply chains and push costs back up again.
In an increasingly volatile global market, all automakers need to know where and how they can save money throughout the EV production process. Automotive World asked industry stakeholders and subject experts to identify some of the best opportunities for cost reductions.
Reimagine manufacturing
Giacomo Margiotta-Mills, Transportation & Mobility Industry Director for Northern Europe at simulation software company Dassault Systèmes, says: “The total production cost of an EV can be segmented into R&D, manufacturing, and re-use. While separate, they are also inherently interconnected.
“R&D for EVs is currently very expensive and time-consuming for many Western automakers, sometimes three to five years, and there’s discussion about how to learn from Chinese brands accomplishing it in 18-24 months. That’s a massive cost saving in itself, and modularity through multi-vehicle platform architectures can help reign in the manufacturing costs of EVs and software-defined vehicles even further. It brings economies of scale, efficiency, and the ability to re-use resources across a wide range of vehicles.
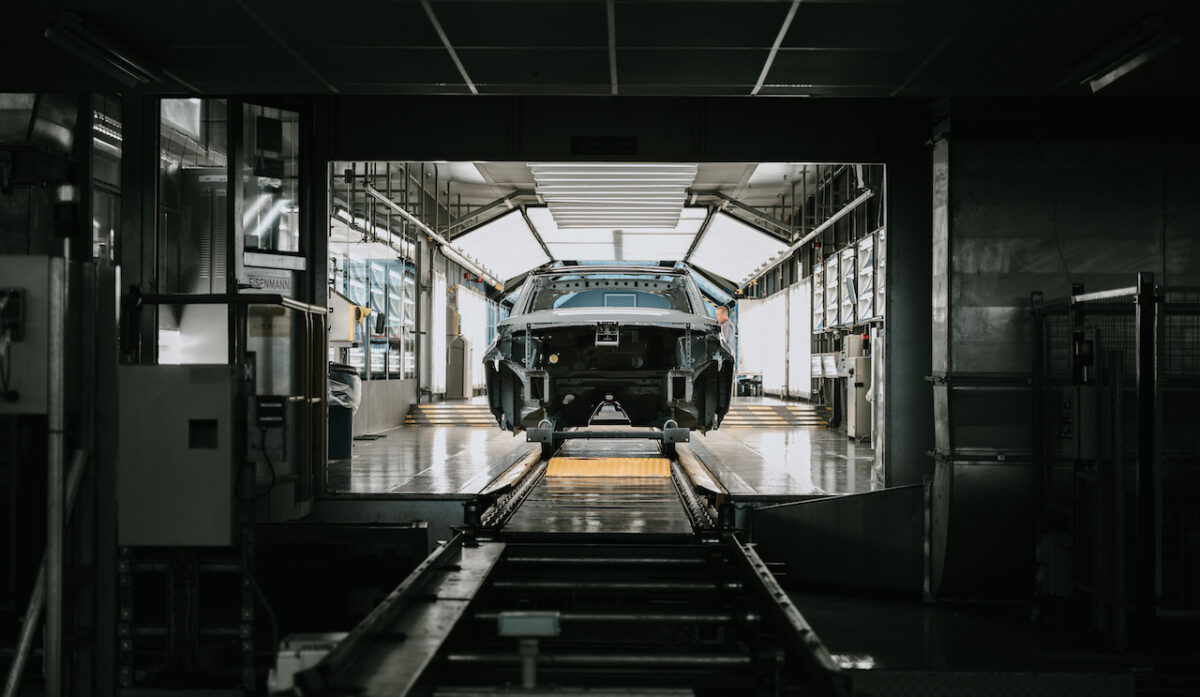
“Virtual twins combined with artificial intelligence (AI) are the common threads that can bring all of this together in EV production. The battery is sometimes up to 40% of a vehicle’s total cost, so using virtualisation to optimise according to specific strategic goals—safety, sourcing, performance—mitigates the high expense of real-world testing. With AI trained to identify the easiest chemistries to manufacture and how a cell will perform throughout its life, including second-life applications, automakers can produce EVs cheaper but also better.
“Those cost savings will originate in battery manufacturing initially, but I expect to see the same thinking applied everywhere eventually. Companies using our 3DExperience platform, such as Jaguar Land Rover, are using virtual twins in a much broader and more ambitious way than manufacturers have done before.”
Consider new materials
Vincent Ledoux Pedailles, Chief Commercial Officer at battery anode producer CarbonScape, says: “As automakers look to cut EV production costs, many are still struggling to do so in a way that’s both financially viable and environmentally sustainable. Much of the challenge stems from costly battery materials and complex global supply chains heavily dominated by China, yet few companies are exploring alternative ways to source the critical minerals needed for EV batteries.
“Biographite, a carbon-negative alternative for the lithium-ion anode market, which can be made locally from woodchips, could be key to solving this challenge. Beyond the environmental benefits, it offers manufacturers a chance to lower production costs thanks to a readily available, low-cost biomass feedstock. Without compromising on performance, biographite also helps automakers avoid trade risks and reduce import and freight expenses.
“Ultimately, by embracing domestically sourced battery materials, automakers won’t just boost long-term resilience and cost efficiency, they’ll also bring key components of EV production back home, contributing to a more sustainable future.”
Boost quality control
Philippe Arsonneau, Senior Vice President of Infrastructure and Power Systems at energy management and automation specialist Schneider Electric, says: “Historically, the battery pack represents the lion’s share of an EV’s cost. Compounding this, current mature battery factories face significant scrap rates, ranging from 6% to 15%, due to quality issues detected late in the process. For newer entrants, these figures can be considerably higher. Addressing this head-on offers a direct and substantial lever for cost reduction.
“Integrating advanced AI-powered quality control throughout the battery production process can enable real-time defect detection and prevention. This means fewer faulty cells, reduced material waste, and ultimately, lower battery costs. This focus on ‘first-time-right’ manufacturing is paramount in making EVs more affordable.
“Beyond optimising the production process itself, another critical area for OEMs to prioritise is implementing advanced predictive maintenance strategies across their manufacturing operations. Unplanned downtime is a significant cost driver in any industrial setting, and EV manufacturing is no exception.
“Remote monitoring, expert analysis, and predictive algorithms can anticipate potential equipment failures before they occur. This condition-based maintenance approach can drastically reduce electrical failure risks by up to 75% and cut unplanned downtime and on-site activities significantly—by as much as 40%. By ensuring continuous operation and minimising disruptions, OEMs can achieve substantial cost savings and improve overall efficiency.”
Prioritise efficient production
Emile Naus, Partner at management consultancy BearingPoint, says: “Manufacturers need to do everything they can to make more EVs more efficiently. The number one cost factor is still batteries, so reducing their weight and expense while improving performance will yield the quickest savings. Achieving these could mean rethinking entire EV designs, but the positive is that even minor tweaks can snowball. For example, altering aerodynamics slightly could mean reduced overall power consumption and therefore smaller, lighter, and cheaper batteries.
Manufacturers need to do everything they can to make more EVs more efficiently
“Efficiency also applies to how automakers leverage partnerships with their suppliers. Put simply, if something isn’t critical to the customer’s direct experience of a brand, OEMs should explore opportunities for collaboration. Fundamental options include the chassis, battery, and drivetrain. The more costs can be shared across an ecosystem, the cheaper each vehicle will be to produce, particularly if developed on multi-vehicle platforms.
“In terms of streamlining manufacturing itself, gigacasting has promise but it’s not the only solution available. EVs have fewer components and can therefore be made on simplified production lines that are easier to automate. Some of the segment leaders offer limited personalisation options, opting to focus more on software-driven differentiation instead of hardware. This opens up plenty of new revenue opportunities, and EVs that are designed to last longer through regular software updates could reduce manufacturing costs simply by producing fewer vehicles.
“However, while software might help automakers save money producing EVs, there is a big cultural challenge attached. They will need to accept a new normal of selling fewer vehicles at a higher price and with a longer lifespan, during which brands can continuously generate new value. Messaging to shareholders would need to be carefully considered.”
Focus on energy
James Crosby-Wrigley, Head of Sustainability at energy specialist Advantage Utilities, says: “OEMs are experiencing a lot of problems beyond their direct control, including import tariffs and the wholesale costs of raw materials. It’s important for companies to focus on what they can influence directly; not necessarily manufacturing processes, but rather the overall efficiency of factory infrastructure.
“Energy—electricity, gas, etc.—is typically the third-highest cost of production, and audits can be carried out to determine where savings can be made. For example, has factory lighting been switched to LEDs, or can the implemented metering solutions effectively determine how energy is distributed around the site? Asking these kinds of questions can identify low-hanging fruit in the first instance, like out-of-hours energy wastage and opportunities for reducing idle time. Going forward, companies can pursue greater energy self-sufficiency by incorporating proximate solar panels, wind turbines, and hydrogen electrolysers. Current estimates suggest approximately 25-30% of an OEM’s energy could be self-generated using renewable energy.
“Following these solutions will always help make manufacturing cheaper, particularly during times of volatile energy prices. A relatively inefficient site could see improvements of 35-40%. As more automakers focus on energy efficiency, I think we could see more activity in self-generated clean energy projects for factories.”