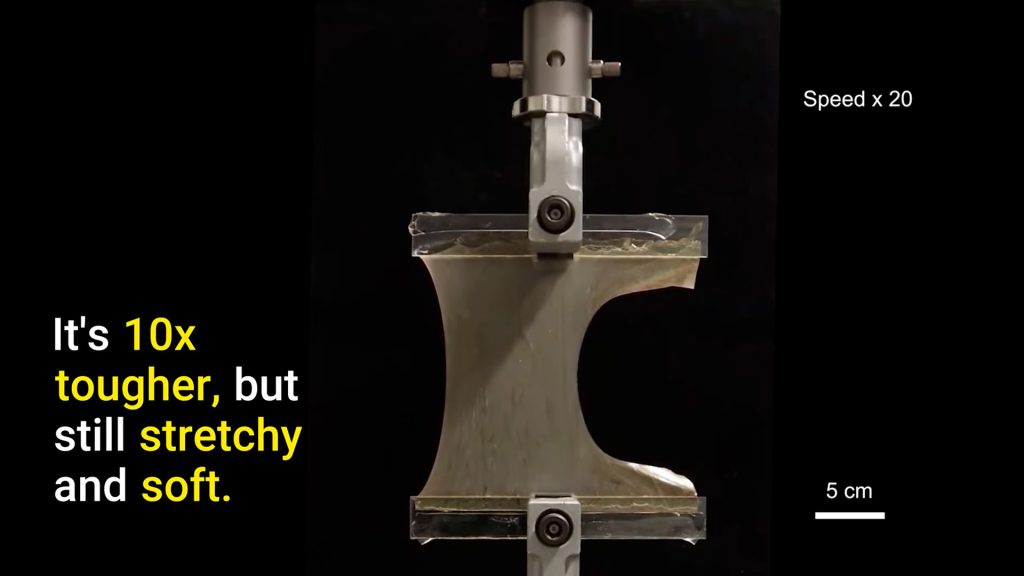
Natural rubber is a wonder material. Few discoveries or innovations come close to its impact on manufacturing, and the car industry is just one of many that depend on it for critical components, such as gaskets, seals, and tires. There’s just one problem: It cracks, and once that happens, it’s not good for much. That’s why researchers at the Harvard School of Engineering and Applied Sciences started tooling around with natural rubber here recently to see if they could make it more durable. And what do you know, they were able to make it 10 times tougher than before with a tweak to the vulcanization process.
See, the science involved in vulcanized rubber production hasn’t changed much since Charles Goodyear patented it in 1844. You start with natural rubber latex that comes from Hevea trees, and once it’s harvested, it’s coagulated, dried, mixed with additives, shaped, and heated. The high-intensity process forms short polymer chains within the material, as the Harvard SEAS writes, resulting in chemical bonds.
The Harvard scientists had an idea: “What if we’re gentler with it?” Sounds crazy, I know, but that one tweak brought about a result that surprised even their bright minds. It was instantly four times better at resisting slow crack growth, even after repeated stretching.
“We imagined that the properties would be enhanced maybe twice or three times, but actually they were enhanced by one order of magnitude,” said Zheqi Chen, a former SEAS postdoctoral researcher and first co-author of the paper.

The change in process, which was based on latex processing methods, preserved the long polymer chains rather than forming shorter ones. Long “tanglemers” inside the material resemble spaghetti noodles rather than a tightly-bound grid. Stress is then able to be spread out across those tanglemers, greatly improving its resistance to cracking and snapping.
Not only is it more resistant to cracks, but it becomes tougher under the conditions that would normally cause natural rubber to fail. It wouldn’t be accurate to call the material “self-healing,” but as the new rubber stretches and small cracks form, those spaghetti tanglemers allow more crystallization. That means the overall strength increases under those circumstances.
This video demonstrates it well:

This process isn’t especially well-suited to automotive applications like tires, at least in its current form. Water evaporation is high, yielding a smaller volume of material than companies would want to wrap around a car’s wheels. The Harvard SEAS writes that, for now, it’s better suited for gloves and other thin applications. You can fill in the blank there, but if scientists can find a way to upscale the process so that it works for automotive seals, then it could be good news for people in sunny climates some 10 to 15 years later.
All the people in Phoenix are hoping that the time comes sooner rather than later.
Got a tip or question for the author? Contact them directly: [email protected]